大企业优先降小成本
作者:姜上泉 226
导读:一家中国民营企业500强,6年时间通过小创新小改善降低成本近4亿元。6年时间,他们实施了23149项创新改善,创造了38747万元的降本成果,这是聚沙成塔,集腋成裘的经典见证。
我们习惯于通过四级创新改善来推动企业的降本增效。什么是四级创新改善?高层通过系统创新改善来推动公司级降本增效项目,中层通过专业创新改善来推动部门级降本增效项目,基层通过自主创新改善来推动班组级降本增效项目,全员通过快赢创新改善来推动瓶颈级降本增效项目。
所谓的系统创新改善,就是瞄准公司级的大课题,组建跨部门团队攻坚克难,即华为所说的端到端的改善,但这种端到端的改善要有好的前提条件,如企业最高决策层的充分支持,中高层经管人员的统一思想,各个部门之间良好的协作文化,激励机制下的高效执行力。如果缺少这些前提条件,端到端的系统创新改善是很容易失败的。
因此,大企业刚开始导入降本增效项目或精益管理项目,我们建议先易后难,先小后大,先短后长的循序渐进式推进,当这种小创新小改善有效消除了小浪费和小损耗,星星之火形成了燎原之势时,大创新大改善自然而然就呼之欲出了。
今天,我们分享一家中国民营企业500强的案例,看看这家集团如何通过小创新小改善达到大降本大创值的。
案例背景
某企业是中国机械工业重点骨干企业之一,总资产超过100亿元,拥有农业装备、环卫装备、汽车制造、现代农业等产业。
然而,深耕农业装备、环卫装备、汽车制造等产业,需要巨大的研发投入,虽然公司的优质产品频频出现在央视的报道中,但公司的净利润率却始终没有突破提升。
2010年,我到这家机械制造企业讲了一场降本增效400多人的大课;2011年,这家企业全面启动了精益管理、降本增效的系列创新改善。
创新改善是只有开始没有结束的旅程。
时至今日,这家机械制造企业的创新改善已经成为公司文化中最重要的DNA。记得2011年到2016年的6年时间里,这家机械制造企业实施了23149项创新改善,降低成本38747万元。
这家机械制造企业的创新改善是如何形成文化并创造良好财务效益的?
我整理出他们重点做的三件事:
一、挂牌成立劳模创新工作室,制定技师创新改善的执行制度和激励制度,每年开展产品创新、技术创新、管理创新项目的申报、立项、评选和发表,并每年开展技术能手比武大赛。
二、公司颁布《持续改善程序》,规定创新改善的提报、评比、验收流程,重点设置创新改善积分制度,创新改善的数量和质量与员工的晋升、津贴、奖金挂钩。
三、各个事业部的各个部门,依据业务实际中存在的浪费和损耗制定《精益改善力》的训练教材,明确“认识浪费、发现浪费、改善浪费”的方法、工具、流程,并对全员进行训练和通关考核。
案例剖析
改善一日易,维持百日难;改善固然可喜,维持更是可贵。
看完这家机械制造企业降本增效之创新改善的做法,好像觉得没有什么特别的亮点,仔细想想,他们优先解决了创新改善中员工“不愿、不会、不能”中最重要的“不愿”,当“不愿”的问题解决了,“不会、不能”的问题就迎刃而解了。
降本增效的创新改善,被挤压出来的员工干劲不会长久,只有员工心底里认同的事情才能够持之以恒。
当创新改善积分制度之创新改善的数量和质量与员工的晋升、津贴、奖金挂钩时,员工们的创新改善意愿就由被动创新改善发展到主动创新改善,由主动创新改善发展到主导创新改善。
降本增效之创新改善,先人后事,人在事前,先解决人的意愿问题,就会起到事半功倍的效果。
这家机械制造企业的创新改善能做到十年如一日的坚持,并在坚持中不断精进,还有一个至关重要的原因就是集团负责人的高度重视和亲自参与,集团每年举办的各种创新改善活动,集团董事长和总经理都会亲自参加。
降本增效导入的有效性=工具方法论×全员参与度×团队领导力。毫无疑义,降本增效项目的成功,这家机械制造企业的团队领导力是压舱石。
6年时间,这家机械制造企业的创新改善能够创造近4亿元的财务效益,除解决了人的“不愿”以外,还有效解决了人的“不能”。
记得2011年到2016年的6年时间里,集团组织各业务部门编写了10多门《精益改善力》的训战教材,开办了10多期《精益改善力》的系列培训,培训结束后组织了10多次学以致用项目评审会和成果发表会。
在编写《精益改善力》系列教材时,集团明确要求教材内容必须来源于本公司业务,用于本公司业务,指导本公司业务;不得抄袭,严禁复制。
在培训《精益改善力》系列课程时,集团明确要求知识要转化为行为,行为要转化为绩效;培训完成才是开始,成果达标才是结束。
无论是降本增效项目还是精益管理项目的推行,员工不愿做用激励,员工不会做用培训。这家机械制造企业降本增效的成功之处就是解决了人的“不愿”和“不能”;比创造近4亿元财务效益更为可贵的是通过降本增效之创新改善,在实践中培养了人才,激发了士气。
降本增效短期靠工具,中期靠人才,长期靠激励。
案例启发
三大创新改善齐头并进
这家机械制造企业每年开展产品创新、技术创新、管理创新项目的申报、立项、评选和发表,通过技术创新抢占经营高度,通过管理创新保持经营高度。
很多企业在降本增效过程中推进创新改善,多数是现场创新改善和管理创新改善,而真正涉及到产品成本的产品创新改善和技术创新改善却廖廖无几。
这家机械制造企业刚开始主要由生产现场的操作员工和基层管理人员做一些六大损失和七大浪费的快赢改善,后来,逐渐发展到以技术人员为生力军的创新改善。
虽然一家企业技术员工人数只占5%-10%,而正是这仅占5%-10%的创新型技术人才推动了企业的可持续增效和降本。
三级经管人员共同参与
小创新小改善用卡,中创新中改善用表,大创新大改善用书。“卡”即创新改善纸卡,重点是填写简单操作方便;“表”是创新改善项目表,重点是要能用一页纸管控好整个项目;“书”是创新改善项目方案书,重点是要能明确跨功能项目小组的责、权、利。
基层主导推动小创新小改善(自主创新改善),中层主导推动中创新中改善(专业创新改善),高层主导大创新大改善(系统创新改善)。
创新改善不是靠“1个不平凡的人”,而是靠“100个平凡的人”。全员创新改善是一个人辛苦前进的100步,变成每个人前进的 1步。
这家机械制造企业降本增效之创新改善的成功之处就在于夯实小创新小改善的基础上发展到全系统创新改善。
为什么是优先降小成本
大企业优先降小成本,这里的小成本即小浪费、小损耗;通过持续推动小创新小改善来消除这些小浪费、小损耗。
曾经有管理咨询界的朋友对我说,降本增效要从“痛点”出发,如新产品的试产与量产是痛点,如新产品的低销量低毛利是痛点,如老产品的品类优化料号优化是痛点,如老产品的高成本高损耗是痛点,我们就从这些“痛点”开始做革新做改善。
但是,我们应该明白,冰冻三尺非一日之寒,滴水石穿非一日之功,这些“痛点”往往是大课题,需要跨部门系统协同才能解决,如果企业内本位、官僚、部门墙严重,这样的“大课题”在短时间内无法取得成效就容易流产。
当然,如果企业内拥有良好的领导力、专业力、协作力、执行力,优先通过端到端系统协同解决这些“痛点”就必然会最快的速度创造最大的效益。
大企业优先降小成本,是因为不少大企业部门墙严重,先通过小创新小改善让员工参与降本增效,在取得一定成绩后再向大创新大改善突破提升,这大概是这家机械制造企业降本增效之创新改善最值得我们借鉴的地方。
2022年5月15日稿
作者简介:
姜上泉,近20年来成功为100多家全球企业500强、中国企业500强进行培训和辅导,曾受邀为北京大学、清华大学、中山大学、上海交通大学等多所著名大学授课。
其拥有自主知识产权的培训、咨询产品贯通企业经营管理的3个阶层,高层通过《利润空间—降本增效系统》学经营、做操盘;中层通过《业绩突破—精益管理系统》学管理、做改善;基层通过《夯实基础—卓越班组系统》学执行、做标杆。
说明:姜上泉导师原创文章,引用与转载请注明出处和作者。
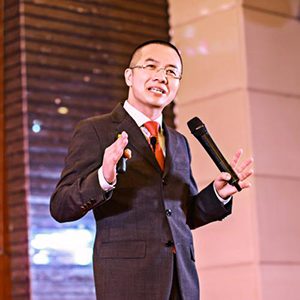
扩展阅读
中小企业招聘广告的内容完善 2024.11.15
对于求职者来说,简历就是敲门砖,对招聘的企业来说,招聘广告就是公司的旗帜,是否足够大,是否活跃,是否能吸引人。结合中小企业自身的实际状况,以及求职者,尤其是00后求职者的特点,在招聘广告内容设置上,可
作者:潘文富详情
倒逼成本管理—降本增效中国行第247 2024.09.29
2024年9月19日—9月21日,姜上泉导师在苏州主讲第247期《利润空间—降本增效系统》3天2夜方案训战营。中集集团、中盐集团、中国建材、花园集团、深南电路、中原证券、空军装备5720等多家大型企业
作者:姜上泉详情
中小企业员工职业生涯规划与管理(企业 2024.05.25
随着“知本时代”的发展,员工越来越关注个人成就感,越来越注重个人职业发展,,而企业也为赢得人才、留住人才,实现平衡发展与人力资本的最大化,员工职业生涯发展规划也受到重视,并成为企业人才战略的重要一环。
作者:李庆军详情
快速提升企业资产效率—降本增效中国行 2024.05.17
2024年5月8日—5月10日,姜上泉导师在深圳主讲第234期《利润空间—降本增效系统》3天2夜方案训战营。中国外运、陕投集团、美卓集团、温氏集团、岗宏集团、开立股份、深圳第一健康医疗集团、深圳英驰供
作者:姜上泉详情
降本增效咨询培训:厦门市降本增效系统 2023.11.06
2023年11月3日—11月4日,在美丽的厦门海滨五星级万丽大酒店,来自福建省15家企业的董事长、总经理带领其高管团队共计60多人参加厦门市降本增效系统企业家研习营。研习中,姜上泉导师重点分享了降本增
作者:姜上泉详情
京刚「说」未来:企业数字化转型受哪些 2023.11.01
中小微企业是中国经济“金字塔”的塔基,是支撑社会发展的生力军。在数字化浪潮下,中小微企业要想实现质的有效提升和量的合理增长,必须加速数字化转型,充分发挥数字经济的赋能效应。然而,中小微企业数字化转型仍
作者:王京刚详情
版权声明:
本网刊登/转载的文章,仅代表作者个人或来源机构观点,不代表本站立场,本网不对其真伪性负责。
本网部分文章来源于其他媒体,本网转载此文只是为 网友免费提供更多的知识或资讯,传播管理/培训经验,不是直接以赢利为目的,版权归作者或来源机构所有。
如果您有任何版权方面问题或是本网相关内容侵犯了您的权益,请与我们联系,我们核实后将进行整理。
- 1姜上泉老师:天海集团 6
- 2不讲道理才是硬道理 165
- 3HP大中华区总裁孙振 235
- 4经销商终端建设的基本 90
- 5姜上泉老师人效提升咨 102
- 6姜上泉老师降本增效咨 101
- 7中小企业招聘广告的内 27421
- 8姜上泉老师:泉州市精 228
- 9姜上泉老师降本增效咨 14752