消除七大浪费确保生产降本增效
作者:姜上泉 383
原创: 姜上泉 降本增效咨询专家姜上泉
导读:和稍微有些资历的生产管理人员谈七大浪费,他们会觉得你“低端”与“脑残”。七大浪费,我们很早就知道了。于是,便看到企业内到处都是“知道了”的南郭先生,现场也到处都是七大浪费。
丰田生产方式创始人大野耐一曾经说过:“没有比完全意识不到问题的人更有问题”。员工的问题意识有多强,企业的改善就能做多大。
我们先由一个故事开始我们的话题。
一批中国培训专家去德国交流学习时,德国培训专家说:“你们中国人很聪明”。
中国培训专家听完后很得意。
德国培训专家接着说:“你们中国人做培训,一场本来要花10个小时学完的课程,你们1小时就学完了,由于学得似懂非懂,实践时问题频发,又花上10个小时甚至更长的时间来分析与解决问题。而我们德国人做培训,10个小时的课程就扎扎实实学习10个小时,操作时基本上就能一次做到位”。
中国培训专家听完后哑然。
我们谈的七大浪费,绝不是1个小时或10个小时能完全说清楚的,今天,我们仅从“了解七大浪费、寻找七大浪费、改善七大浪费”这三点进行简要的阐述。
一.了解七大浪费
我们有些企业的生产管理人员觉得“七大浪费”是陈词滥调,甚至对此不屑一顾,但是,我们要思考的问题是生产管理不改善七大浪费我们还能够改善什么呢?
理解和识别浪费是消除或者减少浪费的第一步,只有了解了浪费,才能够去改善。
七大浪费中,最大的是“过早与过量生产的浪费”,为什么是“最大”?因为它会产生新的浪费,如库存的浪费和搬运的浪费;最恶的是“库存的浪费”,库存会使资产贬值,是企业综合管理能力乏力的体现;最长的是“搬运的浪费”,受布局的影响,改善需要花费较长的时间;最显的是“等待的浪费”,员工们眼睛都能看到却不进行改善,把异常变为正常;最多的是“动作的浪费”,企业里任何地方都存在着这种浪费;最深的是“加工的浪费”,质量标准过高导致过分精确的加工,作业程序过多造成多余的加工;最劣的是“不良品的浪费”,犯了最低级的错误做出残次品,将金钱直接丢进了垃圾桶。
丰田公司提出七大浪费后,后来又提出了第八大浪费,丰田公司认为:“员工的创新和改善是最有价值的资产,不懂得利用员工的脑力资源为最大的浪费”。
不管是七大浪费还是八大浪费,在流程型生产企业和加工装配型制造企业都存在,只是各种浪费在不同生产特点的企业的强弱会有所不同,了解自己企业的主要浪费是哪些并针对性予以改善是我们生产降本增效持续努力的方向。
二.寻找七大浪费
日本著名经济学家藤本隆宏曾经这样评价丰田生产方式的强处:“因为反复发现问题和解决问题,所以没有了问题反而感到不安,于是大家竭尽全力搜寻问题,数万名的职员,处在中毒上瘾一般搜寻和解决问题的状态,这就是丰田生产模式的真正过人之处”。
而丰田生产方式创始人大野耐一则这样说道:“判断一家企业的管理水平,通常管理者谈话的前5分钟内就谈到改善,前10分钟内就谈到现场,则可论定这是一家好公司”。大野耐一同时又说:“剔除浪费并不难,难的是如何发现浪费”。
然而,我们很多企业的管理人员和员工为什么不能够尽早的发现浪费和改善浪费?甚至于对浪费视而不见,归根结底主要原因有三点:
1.对浪费无动于衷
记得有一次和一家企业的总经理一起到生产现场,总经理生气地质问生产经理:“为什么我每次到生产现场都能发现这么多浪费,你为什么就发现不了?”生产经理当即回答道:“总经理,您能发现浪费,是因为您平时很少下现场”。这句话差些当场就把总经理给气晕,生产经理的言下之意就是我发现不了浪费,是因为天天在现场,麻木了和习以为常了。
如果你不能发现问题,你就是最大的问题。对浪费和问题麻木不仁和视而不见的管理者,要么是能力不足,要么是态度不正,他们才是企业“最贵”的浪费。
2.害怕暴露出浪费
一次咨询项目月度总结会上,车间主任正在汇报如何发现和改善生产过程中的浪费,在场的董事长听了打断汇报很不高兴地说:“你们今天才发现和改善这些浪费,前些年你们干什么去了?”
董事长的这一句话,就等于扼杀了员工们今后的创新改善意愿,既然改善浪费会遭到责骂,不改善反而平安无事,那么,员工们为什么要改善呢?
不少企业的管理人员害怕暴露问题和浪费,他们担心因此而受到上司的批评和处罚,我们企业的经营者和管理者应该拥有健康的精益思想,那就是“多鼓励,少批评,用欣赏的眼光看待员工们的每一项改善”。
3.缺乏改善激励机制
员工们不能有效地发现浪费和改善浪费,要么是没能力,要么是没意愿,除此之外,没有其它原因。能力不足靠训练,意愿不足靠激励。
要提高员工们发现浪费与改善浪费的能力,我们就有必要训练管理人员和员工们七大浪费、六大损失以及一些基础的IE改善知识。
要提高员工们发现浪费与改善浪费的意愿,我们需要做好五件事情:①.简化改善的申报程序;②.缩短改善奖励的周期;③.公开改善奖励的仪式;④.改善立项纳入干部考核;⑤.最高层参与改善成果的发表。
不得不说公司最高层参与改善成果的发表是改善过程中最好的激励,我曾经在全球500强企业日资住友电工训练期间,看到每个月的改善成果发表会总经理都会亲自参加,而且多年来他都是这样坚持做的;我询问他们的一些管理人员,总经理能听懂中文吗?他们说不完全能听得懂,但总经理就是这样静静地坐着、看着、听着,而且每次他都会来。记住,支持不是停留在口头上,更重要的是在行动上。总经理关注的重点在哪里,改善的绩效就在哪里。
现在,我们明白了员工们为什么不能够尽早的发现浪费和改善浪费的原因,那么,我们到现场如何快速地发现和寻找出浪费呢?最基本的方法就是“三现原则”和“望、闻、问、切”。所谓的“三现原则”就是“到现场,看现物,了解是否适合现状”;而“望、闻、问、切”则指的是“观其形,听其言,问其痛,把其脉”。
“望”的重点是到生产现场后,看精益的布局是否合理,看流程中是否有断点,看是否形成边续流,看是否有人员等待和物流停滞,还要看在制品库存的数量。记住,一个精益的布局流程能在设计的源头上消除很多的浪费,一个在制品库存量高的现场一定存在着计划不均衡和产线不平衡的问题。
“闻”的重点是到生产现场后,听前后工位员工们反馈的问题,听跨部门员工(如QE、PE、IPQC等)对现场的抱怨,听生产部门主管对现场的期待,从与他们的交谈中捕捉到浪费点和改善的需求。
“问”的重点是到生产现场后,对每一个浪费作业需要反复提出为什么(WHY),以找出浪费最根本的原因。怎么通过“问”寻找出浪费呢?问其Q/C/D/S/M达成现状与公司目标及竞争对手的差距,问其4M1E各个环节中存在的问题,问其哪些工序可以实施ECRSI改善。
“切”的重点是到生产现场后,调阅与分析KPI数据达成情况,测量员工实际作业工时与标准工时的差异,观察设备运行的工艺参数是否符合标准工艺参数的要求。
通过“望、闻、问、切”,我们就可以很快的找出现场的各种浪费,记得松下电器的一位日方总经理曾经对我说:“你越是IE专家,你就越找不出浪费,因为IE专家首先想到的是如何去改善,而不是寻找浪费”。
改善浪费具有三个层次:浪费找员工、员工找浪费、员工具备改善浪费的能力。我们要改善浪费,就必须先学会发现浪费,这一点我们切不可本末倒置。
三.改善七大浪费
可口可乐公司有一句经典语录:“管理者不改善不创新就是工作失职”。一流的企业没人知道有浪费,人人改善浪费;二流的企业有人知道有浪费,有人改善浪费;三流的企业人人知道有浪费,没人改善浪费。
我们习惯于把生产中的作业分为3大部分:增值的、不得不做的浪费、无效的浪费。无效的浪费我们要做改善,增值的作业我们也要做改善。
消除浪费一般有四大步骤:①.了解什么是浪费;②.识别工序中哪里存在浪费;③.使用合适的工具来消除已经识别的特定浪费;④.实施持续改进措施并重复执行上述步骤。
在消除浪费的过程中,我们还应该遵循“浪费改善先宏观后微观,先整体后局部;浪费改善大处看布局和流程,小处看工序和动作”的原则实施改善。
针对布局和流程这些较大的浪费,我们可以运用系统改善的方法进行突破,如“VSM、DMAIC、OPF、Pull、Kanban、均衡生产”等;针对工序和动作这些较小的浪费,我们可以运用专业改善和自主改善的方法进行突破,如“QCO、SMED、PTS、8D法、A3报告、创意功夫等”。
想法是提案,实践是改善。用我们的眼睛去发现浪费,用我们的双手去改善浪费。烛光般的改善,可以带来阳光般的成果;精益改善我们既要推崇革命性的大改善,还要强调积小改善成大创新的持续改善。
大野耐一曾经这样说过:“假如企业的商品售价中成本占90%,利润为10%,把利润提高一倍的途径有两种:①.销售额增加一倍;②.从90%的总成本中剥离出10%的不合理浪费”。
减少10%的浪费可以实现利润翻番,看来,生产部门要做好降本增效,最直接的还是消除七大浪费。另外,我们特别告诫企业的经营者,除非您企业已经把不增值的活动降低到一个与VA相当的平衡点,否则,不要花钱去投资固定资产。要不然这种投资失误,将会造成企业巨大的成本浪费。
2018年10月21日稿
说明:《利润空间—降本增效系统》创始人姜上泉导师原创文章,引用与转载请注明出处和作者。
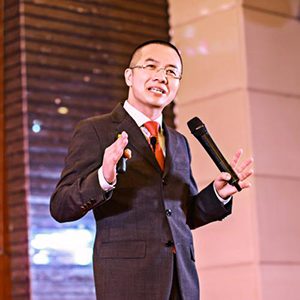
扩展阅读
姜上泉老师:天海集团精益领航项目启动 2025.02.10
2025年2月5日,世界500强广州工控集团旗下天海集团精益领航项目启动,集团董事长致辞,集团总裁助理宣布了项目组织管理制度,集团副总裁、20家分公司总经理及130多位经管人员参加了项目启动会议。天海
作者:姜上泉详情
姜上泉老师人效提升咨询培训:济南市人 2024.12.16
2024年11月29日—30日,姜上泉导师在济南市人效提升1000人大会分享《六步人效提升》,来自山东省各地市的900多位企业代表及中国重汽、日立电梯、万达控投、齐鲁制药、新华制药、鲁南制药、临工集团
作者:姜上泉详情
姜上泉老师降本增效咨询培训:中航工业 2024.12.16
2024年12月6日–7日,姜上泉导师在北京中国航空工业集团H公司训练辅导降本增效系统。H公司董事长、党委书记及50多位经管及技术人员参加了第250期降本增效方案训战营。2天1夜降本增效训战辅导,姜上
作者:姜上泉详情
姜上泉老师:泉州市精益六最系统研习 2024.11.15
2024年11月8月—9日,姜上泉导师在泉州市主讲《业绩突破—精益六最系统》,来自闽南地区40多家企业的100多位经管人员参加了训战研习。训战开始,姜上泉导师首先分享了精益管理之科学系统与哲学系统的运
作者:姜上泉详情
姜上泉老师降本增效咨询培训:洋井石化 2024.11.08
2024年11月1日–2日,姜上泉导师在连云港石化产业基地洋井石化集团训练辅导降本增效系统,石化产业基地国资委领导、洋井石化集团党委书记兼董事长及50多位经管人员参加了训战辅导。连云港石化产业基地是国
作者:姜上泉详情
倒逼成本管理—降本增效中国行第247 2024.09.29
2024年9月19日—9月21日,姜上泉导师在苏州主讲第247期《利润空间—降本增效系统》3天2夜方案训战营。中集集团、中盐集团、中国建材、花园集团、深南电路、中原证券、空军装备5720等多家大型企业
作者:姜上泉详情
版权声明:
本网刊登/转载的文章,仅代表作者个人或来源机构观点,不代表本站立场,本网不对其真伪性负责。
本网部分文章来源于其他媒体,本网转载此文只是为 网友免费提供更多的知识或资讯,传播管理/培训经验,不是直接以赢利为目的,版权归作者或来源机构所有。
如果您有任何版权方面问题或是本网相关内容侵犯了您的权益,请与我们联系,我们核实后将进行整理。
- 1姜上泉老师:天海集团 6
- 2不讲道理才是硬道理 165
- 3HP大中华区总裁孙振 235
- 4经销商终端建设的基本 90
- 5姜上泉老师人效提升咨 102
- 6姜上泉老师降本增效咨 101
- 7中小企业招聘广告的内 27421
- 8姜上泉老师:泉州市精 228
- 9姜上泉老师降本增效咨 14752