跟丰田学员工管理
作者:姜上泉 291
导读:《跟丰田学员工管理》这篇文章原创于2009年1月,后来,我也到过丰田的多个生产基地;今天,再次细读这篇文章,仍然能感觉到丰田员工管理的大智慧、大思想。
由若松义人先生编著的《谁都能成为一流员工》是我见到过无数不多的好书,该书全面阐述了丰田员工管理和丰田员工培育的哲学,多次细读这本书后,便将这本书在员工培育和管理上的几个独特的观念进行摘录、整理、修饰、提炼,撰写出《跟丰田学员工管理》这篇文章,与您共飨丰田人才之道。
丰田生产方式是当今全世界各行各业学习的楷模,丰田的成功,核心是人才培育和员工管理的独特哲学。记住丰田的名言:“制造产品就是在培育人才”。“先培育人才,再经营事业,商机由此而生”。
去年冬天(2008年),我在长春做《精益管理实训营》培训,一汽大众的培训部主管询问:“请问老师,丰田公司员工的奖金并不是很高,为什么丰田员工的改善行动力却如此之强呢?”
要回答这个问题,就得了解丰田对员工的管理方式,许多人误认为TPS(JIT)就是直接引进丰田式的经营手段和管理方法,其实,丰田式的改革是从人员培育与人员管理方式开始的,这样,改革才能作为一种文化扎根于企业中。也难怪丰田生产方式创始人大野耐一先生说:“当持续改善已经成为丰田员工的一种工作习惯,就证明丰田式生产已经获得了成功”。
丰田员工管理的独特模式是什么呢?我们从以下三点进行探讨:
一.让员工学会动脑筋
大野耐一先生说:“如果所有工作都由领导者铺平道路,这岂不是无法发挥现场工作人员的智慧了吗”?
先询问大家一个问题,“员工为何懒得动脑”?得到的可能有“工资太低、员工素质差、员工不关心企业”等等答案,看看丰田的说法:“员工懒得动脑的原因是管理者直接下达命令,告诉员工照管理者说的去做”。
直接告诉员工怎么做这样或许可以早日看到改革成果,然而,这样的改革无法真正帮助企业成长,如果各项工作都为员工铺平道路,员工就不会再独立思考问题。即使短期内能够看到成效,管理者一旦离开,企业便会迅速恢复原来的状态。
丰田生产方式最看重的正是让员工“自己寻找答案”。
举个案例:“这条生产线有7名员工,效率太低,请想办法减少到5名”。一位丰田的基层管理人员接到上级的命令,他感到手足无措。于是他只好请求上级给出具体的指示,但得到的答复却是“请你自己寻找答案吧”。
这位基层管理者起初完全不知该从何处下手,于是只好到其他生产线参观,然后再征求上级的意见,如此循环反复,直到寻找到理想的解决方案。这位丰田基层管理者切身体会到:“让员工自己寻找答案,上级加以指点,这种做法非常有利于员工个人的发展”。
丰田改革活动的支柱是“创意提案制度”,让员工感到贡献智慧能实现自身的价值,为了让员工学会动脑筋改善工作现场的不合理,丰田提出了“多提方案比提出好的方案更有价值”的口号。
有些企业无人提出改进方案,这是因为管理者无视员工发现的小问题或来自员工的点滴启示。有些企业的负责人经常抱怨:“我们公司的员工不开动脑筋思考问题”。而员工也颇为不满:“我们公司的管理者根本听不进员工的意见”。在这种情况下,员工和企业就不会发生任何变化。
因此,丰田的高阶管理者经常告诫部属,“不允许对员工的提案,用评论家的口气提出质疑”。“没有代替方案就别轻言反对”。正是这些卓越理念的支持,使丰田的员工更愿意“挖掘”自己的智慧去改善工作现场。
二.“人性化”管理
是否日系企业严格的管理制度没有人性化?是否日系企业森严的等级制度不把员工当人看?多数提问得到的答案几乎都是肯定的。事实上,日系企业是最会把员工当人看的,日系企业是最懂得以人为本的,日系企业员工的能力是高于其他企业员工能力的。
什么是人性化管理?什么是以人为本?
先分析一个案例:某企业交付给客户的产品经常无法正常运转,经检查发现,绝大多数情况都是零件的组装出现问题。而导致这一问题的原因是在装卸和运输的过程中,是轻微的撞击导致零件的脱落。
有三种解决方案:
第一种是用货车运输时派员工同行,卸货后,在交货之前重新检查一遍产品零件的组装情况。
第二种是提醒作业人员注意,把产品组装得更加牢固。
第三种是改进工艺,使零件不会在撞击中脱落。
选择哪种解决方式?多数企业会选择前两种方式,通过强化产品的质量检查以及提醒作业人员注意来解决,但这种解决方式显然是“不人性化”的,这将增加作业人员的注意力和困难度。
所谓“人性化”,主要指不使员工以艰难的姿势作业,以及不让员工从事危险作业。丰田生产方式始终贯彻这一内容。
真正丰田式的“人性化”被称之为“容易上手”。例如,上述案例如果对零件本身进行改进,从而使缺乏经验的人也能轻而易举地完成安装工作。
从这一意义而言,教会作业人员安装的窍门,或是提醒他们边思考边安装,是不能称之为“人性化”的。因为作业中边思考边判断,是很容易出现错误的。
或许我们可以把丰田式的人性化理解为“傻瓜式的工作方式”。通过傻瓜式设计使员工更容易作业,又通过员工创意提案活动、TPM活动、QCC活动让员工充分发挥其聪明才智参与工作改善,这一套员工管理方式,才称得上名副其实的“人性化管理”。也难怪大野耐一先生说:“让每一位员工实现个人价值,员工不应只是被视为会用双手干活的工具,而更应该被视为一种丰富智慧的源泉”。
以人为本,如何发挥员工的智慧是一切工作的基础。
三.与员工面对面沟通
丰田有一句话叫“成为值得员工信赖的领导者”。丰田生产有不少词语强调人与人之间合作关系的重要性,如“不要离群索居”、“开展互助活动”等。这些话语中透露出的信息其实都离不开与员工有效的沟通方式。
理光公司的滨田广会长认为,要想让“员工满意”,必须先让“员工理解”。这一句真是一针见血。
分享一个案例:某企业推行TPS生产方式,遭遇到员工的强烈抵制,他们认为,TPS生产方式提高了生产效率,就要减少工作人员,自己就会丢掉工作。有一天,他们向工厂负责人提问:“这么改下去,最后就不需要我们了吧?”因此,大家自然会认为“TPS就是为了裁减人员”。
如果企业负责人没有面对面向员工解释清楚这样做的原因,TPS的推行就注定失败。
与员工面对面沟通,让每一个人在充分理解的基础上开展工作,这样的改善是容易开展下去的。因此,丰田鼓励管理人员多到一线现场倾听、询问。
例如,标准作业规范是必须遵守的,但另一方面,员工在工作中会遇到各样的情况,于是他们独立思考改进方案,以进一步提高生产效率。通过管理人员与员工一起集思广益,现有的标准作业在不知不觉间转变成了员工自己的工作方式,自己制定的规则,当然容易遵守。
所以,我们常说:“员工认同的事情更容易被员工执行”。
管理人员不要独自冥思苦想现场的改善方法,要养成经常与员工面对面沟通,收集点滴启示,并把启示转变为改善对策的习惯。那些习惯于聆听员工的声音并归纳总结的人,总是能够得到更多的启发。
大哲学家苏格拉底说:“答案尽在问题中”。
管理界流行一句名言:“不会说的不如会说的,会说的不如会听的,会听的不如会问的”。
记住,向员工问问题是没有成本的。
答案就在员工心里,管理人员仅仅需要做的是问正确的问题。
管理者唯一愚蠢的问题就是你不去问。
丰田有一句名言“员工的创新是企业最有价值的资产,不懂得利用员工的脑力资源为企业最大的浪费,激活员工改善的智慧潜能是丰田的核心竞争力”。
管理的第一要素是人(彼得·德鲁克)。
员工管理最有效最恰当的方式就是“发挥员工的智慧,让员工自己找答案”。
说明:《利润空间—降本增效系统》创始人姜上泉导师原创文章,引用与转载请注明出处和作者。
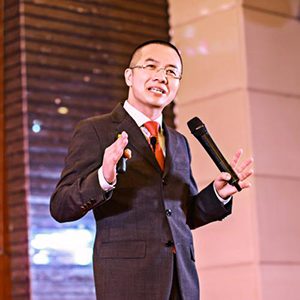
扩展阅读
倒逼成本管理—降本增效中国行第247 2024.09.29
2024年9月19日—9月21日,姜上泉导师在苏州主讲第247期《利润空间—降本增效系统》3天2夜方案训战营。中集集团、中盐集团、中国建材、花园集团、深南电路、中原证券、空军装备5720等多家大型企业
作者:姜上泉详情
优化考核方式,减少员工抵触 2024.08.22
考核,是员工付出和收益之间的一个动态评估机制。理想化的结果是劳资双方都满意——员工活没少干,老板钱没少给。但是,现实中,大多数公司的考核机制很难做到公开、公平、公正。老板总觉得花钱养了一帮废物,而员工
作者:潘文富详情
经销商的产品驱动与管理驱动 2024.07.03
早期的经销商几乎都是产品驱动,运营方式就是卖货,盈利方式就是靠卖货赚差价,然后就是多卖货,卖名牌货,卖新产品,卖高端品。理论上来说,终端覆盖率越高,陈列做得越好,促销活动持续不断,货就卖得越多,钱就赚
作者:潘文富详情
管理寓言故事:挤牛奶的姑娘 2024.06.07
寓言故事:一个农家挤奶姑娘头顶着一桶牛奶,从田野里走回农庄。她忽然想入非非:amp;这桶牛奶卖得的钱,至少可以买回三百个鸡蛋。除去意外损失,这些鸡蛋可以孵得二百五十只小鸡。到鸡价涨得最高时,便可以拿这
作者:李文武详情
00后员工的试用期工资怎么定 2024.06.04
员工来上班,先得把钱的事情说清楚,这个不能模糊。远的不说,这刚入职的试用期工资得要明确。当然了,试用期工资发多少,这个事的主导权在老板手里,老板是怎么想的,决定了这个钱是怎么发给员工的。老板对新进员工
作者:潘文富详情
中小企业员工职业生涯规划与管理(企业 2024.05.25
随着“知本时代”的发展,员工越来越关注个人成就感,越来越注重个人职业发展,,而企业也为赢得人才、留住人才,实现平衡发展与人力资本的最大化,员工职业生涯发展规划也受到重视,并成为企业人才战略的重要一环。
作者:李庆军详情
版权声明:
本网刊登/转载的文章,仅代表作者个人或来源机构观点,不代表本站立场,本网不对其真伪性负责。
本网部分文章来源于其他媒体,本网转载此文只是为 网友免费提供更多的知识或资讯,传播管理/培训经验,不是直接以赢利为目的,版权归作者或来源机构所有。
如果您有任何版权方面问题或是本网相关内容侵犯了您的权益,请与我们联系,我们核实后将进行整理。
- 1不讲道理才是硬道理 165
- 2HP大中华区总裁孙振 234
- 3经销商终端建设的基本 90
- 4姜上泉老师人效提升咨 101
- 5姜上泉老师降本增效咨 99
- 6中小企业招聘广告的内 27421
- 7姜上泉老师:泉州市精 226
- 8姜上泉老师降本增效咨 14752
- 9倒逼成本管理—降本增 18615